Spindelanschluss
Bei nicht durchbohrten Spindeln muss der Vakuumanschluss zwischen Spindelgewinde und dem eigentlichen Futterkörper erfolgen. Dieser Anschluss muss allerdings auch alle Kräfte aufnehmen können, die beim Drechseln auftreten, und muss damit mechanisch recht stabil aufgebaut sein.
Bei durchbohrten Spindeln ist die mechanische Beanspruchung erheblich geringer und ist damit dem 3D-Druck zugänglich.
Eigenbau mit 3D-Drucker
Dieser Spindelanschluss ist für eine Stratos XL entworfen. Er wird am Handrad in die Hohlspindel eingeführt und verbindet die drehende Spindel mit der Vakuumanlage. Die Lagerung des Schlauchanschlussteils ist so leichtgängig, dass das Mitdrehen bereits durch den eingesteckten Vakuumschlauch sicher verhindert wird; eine weitere Fixierung ist nicht nötig.
Dieser Aufbau ist geometrisch recht einfach konzipiert und somit sicher auch aus geeignetem Holz drechselbar.
Die Spindel der Stratos XL hat eine Bohrung von (knapp ?) 16mm; damit ist dieser Spindelanschluss grundsätzlich für alle Spindeln mit diesem Durchmesser geeignet; ggf. müsste die Druckscheibe ans Handrad modifiziert werden.
Die Spindel der Stratos XL ist mit vier radialen, durchgängigen Gewindebohrungen versehen; in diese sind Schrauben zum Zwecke der Drehzahlmessung eingesetzt. Diese können Leckagen verursachen, die ggf. durch ein Abdichten dieser vier Schraubengewinde beseitigt werden müssen .
Für den Aufbau wird benötigt:
- die 3D-gedruckten Gehäuseteile
- ein Schlauchfitting mit 12mm Schaft (www-Suchbegriff: "Druckluftfitting")
- ein Kugellager 6202 2RS (Maße 15x35x11)
- Alurohr 15x2 (Außendurchmesser x Wandstärke)
- 2 O-Ringe 13x1,5
- CA - Kleber
Wir beginnen mit dem Gehäuse.
In das Lagergehäuse wird ein Schlauchanschlussfitting eingeklebt (ich achte auf mechanisch klemmende Fixierung und verwende Sekundenkleber; dieser klebt das gedruckte PLA gut und haftet auch auf dem (vermutlichen) PA des Fittings völlig ausreichend).
Für das Anschlussrohr in die Spindel wird das Alurohr auf 8 cm abgelängt.
- innen sauber entgraten
- im Spannfutter (kurz gespannt) mit Schaber Enden glätten/verrunden
- im Spannfutter lang spannen, Reitstock als Zentrierung gegensetzen, reitstockseitig zwei Nuten eindrehen (schmaler Abstecher) bei 5 mm und 35 mm; Nutgrunddurchmesser 13,2 - 13,3 mm, Breite 1,6 - 1,8 mm; Nutenkanten anfasen
- Rohr umspannen, mit Reitstock zentrieren und reitstockseitig am Ende ca. 12 mm (auf Durchmesser <=15,0 mm) abdrehen (Schaber/Abstecher) und in Kugellager einpassen
- Alurohr (unten bündig) mit geeignetem Kleber in Lager einsetzen (die Achse des Rohrs muss in der Achse des Lagers liegen). Ich habe hierfür ein recht teures Spezialprodukt verfügbar (Loctite 638), aber wenn der Sitz gut passt, sollte dünnflüssiger Sekundenkleber gut funktionieren.
Lager in Gehäuse einkleben (auch hier funktioniert CA-Kleber, allerdings muss darauf geachtet werden, dass man nicht das Lagerinnere damit füllt)
Druckscheibe aufsetzen, O-Ringe fetten und in Nuten einsetzen
Nach Aushärten des Klebers kann der Spindelanschluss in die Spindel eingeführt werden; die Druckscheibe greift dabei um die Fixierungsscheibe des Handrades und zentriert den Anschluss; gleichzeitig überträgt sie die Vakuumkräfte vom inneren Lagerring auf das Handrad und damit auf die Spindel.
Das Abziehen des Spindelanschlusses sollte auch am Druckring geschehen, so vermeidet man eine unnötige Belastung der äußeren Lagerklebung.
Hier sieht man, wie einfach der Spindelanschluss eingesetzt wird.
Im mittleren Filmabschnitt wird die Spindel gestartet, läuft auf 1000 Udr/min hoch (das ist etwas schlecht zu erkennen) und wird wieder abgebremst.
Wie man sieht, ist dabei der im weiten Bogen liegende Schlauchanschluss völlig ausreichend, um ein Mitdrehen des Lagergehäuses zu verhindern.
Bemerkung zu Dichtheit/Enddruck der Vorrichtung:
Das Kugellager selbst weist natürlich eine gewisse Undichtigkeit (Leckrate) auf. Wenn der Spindelanschluss ordentlich aufgebaut wurde, sind alle anderen Undichtigkeiten gegen die Lager-Leckrate vernachlässigbar. Solange diese wiederum klein gegen das Saugvermögen der Vakuumpumpe ist, kann am Vakuumfutter ein guter Unterdruck erreicht werden.
Ich erreiche mit einer 25m³/h-Pumpe am Schlauchende vor dem Spindelanschluss einen Druck von ca. 10mbar abs.; mit dem angeschlossenen Spindelanschluss erreiche ich (aufgrund der Leckage des Kugellagers) noch ausgezeichnete 50mbar abs.
(Die letzte Aussage habe ich mit den von mir verwendeten (günstigen) Kugellagern ermittelt; ob sich alle Kugellager dieses Typs, unabhängig von Hersteller und Fertigungslos, bezüglich der Leckrate genauso verhalten, kann ich nicht sagen.)
Ein Unterschied zwischen statischem und dynamischen Betrieb ist nicht feststellbar.
Dauerbetriebseignung:
Bei einem Betrieb unter Vakuumbelastung und 1400 Udr/min wird das Alurohr (das direkten Kontakt zum Kugellager hat) nur etwas warm; auch nach 20min-Betrieb war keine weitere Erwärmung feststellbar. Dauerbetriebseignung ist damit gegeben.
Spindelanschluss - Variante
Da mir das Einkleben der Kugellagers in das Gehäuse nicht wirklich gefällt, habe ich eine gut druckbare (aber eher nicht mehr drechselbare) Variante konstruiert, die ohne die äußere Lagerklebung auskommt. Dafür kommt ein weiterer O-Ring zum Einsatz. Das Lager wird in einen O-Ring-gedichteten Sitz gedrückt und von einer Deckelmutter fixiert; das erspart diese Klebung und lässt sich sehr einfach montieren.
Benötigt wird neben einem anderen Gehäuse zusätzlich:
- 1 O-Ring 34,5x3,5
Die vakuumtechnischen Eigenschaften waren in meinen Versuchen identisch zur obigen (geklebten) Variante; auch Dauerbetriebseignung ist gegeben.
weitere Spindelanschluss - Variante
Die im Folgenden gezeigte Variante ist für einen realen Betrieb leider nicht geeignet, bringt aber interessante Erkenntnisse mit sich.
Aufbauend auf der O-Ring-Variante sollte die Dichtigkeit des Spindelanschlusses durch Einbringung eines Wellendichtrings verbessert werden.
Das Gehäuse der O-Ring-Variante wurde um einen Sitz für einen Wellendichtring 15x32x5,5 direkt unter dem Kugellager erweitert.
Der Wellendichtring wird mit einem Einpressdorn und etwas Fett eingesetzt.
Das Alurohr muss jetzt lediglich um einige mm unterhalb des Kugellagers "verlängert" werden, um im Wellendichtring zu laufen.
Es wurde diesmal allerdings anders gefertigt. Zwischen Spitzen wurde es von rechts abschnittsweise derart auf knapp 15.0mm abgedreht, bis jeweils das Kugellager eben aufschiebbar war, bis an den Lagersitz ca. 10mm vor dem linken Ende. Das linke Ende wurde als Sitz für den Wellendichtring auf etwas über 15,0mm belassen und geschliffen.
Das Lager wird auf die Welle geklebt, wie gehabt, und die Welle mit Gehäusedeckel, Druckscheibe und O-Ringen vervollständigt.
Die Lippe des Wellendichtrings wird geölt und im Hohllraum des Wellendichtring ein kleines Ölreservoir angelegt, da die Reibung zwischen Wellendichtring und Welle reduziert werden muss und die Abfuhr der Reibungswärme über die Welle und über die Konvektion im Ölfilm stattfindet. Hier liegt sicher ein kritischer Punkt dieser Konstruktion da die Anlage eines großen Ölreservoirs, das normalerweise die Kühlung sicherstellt, nicht möglich ist.
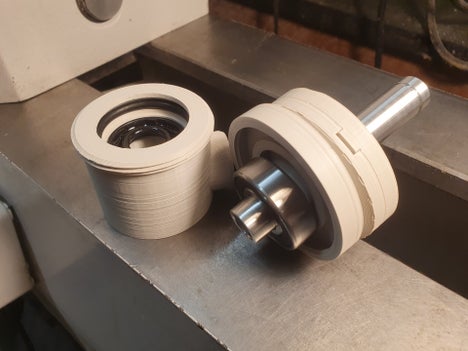
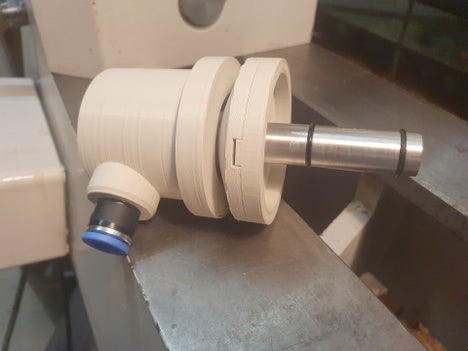
Betriebserfahrung:
Der Spindelanschluss war um einiges schwergängiger, als der ohne Wellendichtring, aber doch noch überraschend leichtgängig, so dass ein Betrieb immer noch nur mit dem angeschlossenen Vakuumschlauch und ohne zusätzliche Fixierung des Gehäuses möglich war.
Die Dichtheit des Anschlusses war um etwa einen Faktor 10 höher als ohne Wellendichtring und der erreichte Enddruck war mit ca. 10mbar abs. nicht mehr vom Enddruck am geschlossenen Vakuumschlauch-Ende unterscheidbar. Das sind soweit ausgezeichnete Ergebnisse.
Leider bestätigte sich im Dauerbetrieb die Befürchtung zu großer Reibungswärme. Nach 10 Minuten Betrieb bei 1400 Udr/min war die Welle bereits so warm dass sie nur gerade eben noch angefasst werden konnte. Im weiteren Betrieb stieg die Temperatur weiter und der Gehäusedeckel begann sich durch das ebenfalls heiß gewordene Lager zu verformen.
Nach dem Zerlegen des Spindelanschlusses zeigte sich bereits etwas schwarzer Abrieb im Öl im Kontaktbereich der Welle zur Dichtlippe.
Ohne eine entscheidende Verbesserung der Kühlung/Schmierung der Dichtlippe scheit mir dieser Aufbau nicht praktikabel.
Erstelle deine eigene Website mit Webador